Pallet Racking Applications
Racking solutions and their applications are wide and diverse.
Select a type of racking to find out more.
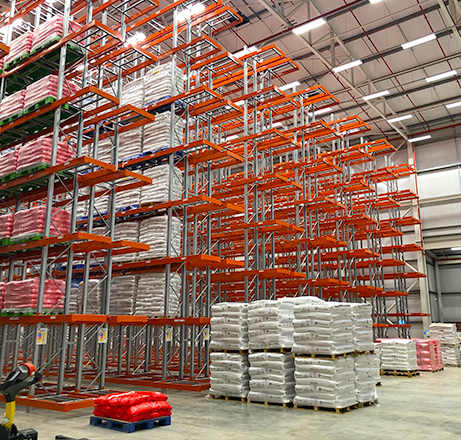
Key Benefits
Well designed and maintained pallet racking systems will be scalable and the right choice of racking partner will have a major impact on the success of your business in the future. Each type of racking fits a specific need within your warehouse. You can find out specific benefits in our Configuration Options below but all racking solutions give you base control to.
- Optimisation – Configure for maximum storage, density and efficiency
- Flexibility – Reconfigure as you grow and change
Configuration Options
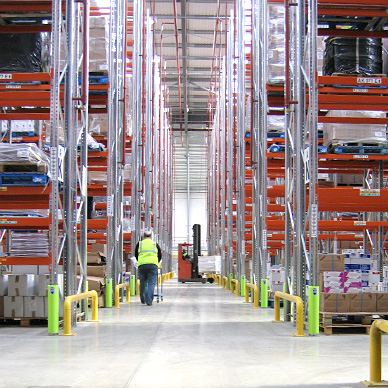
Wide Aisle Pallet Racking Systems
Still the most common form of pallet racking storage: The standard pallet racking layout provides unrestricted access to all pallets. Pallets stored in wide aisle racking are not subject to any restrictions in layout and are freely accessible at all times.
Even in a state-of-the-art warehousing operation the standard pallet racking system is still the most common form of pallet storage. Industry & logistic companies appreciate the versatility of our pallet racking, which can be assembled as single or double depth racks. Available in heights of up to 30 meters and varying depths and widths, our Dexion P90 Wide Aisle Racking will perfectly fit into the space available and is suitable for all kinds of pallets – Euro, Chep, disposable or captive pallets, mesh boxes or bins.
TYPICAL APPLICATIONS
- Manufacturing
- Food and Drink
- National Distribution Depots
- Automotive & Engine
- Food & Drink
- Educational & Office Supplies
- Cold Storage
Narrow Aisle Pallet Racking
Narrow Aisle Pallet Racking is the space-saving option if floor space is limited: maximum storage capacity, fast accessibility to every pallet and quick order-picking straight from the racking.
The main advantage of Narrow Aisle Pallet Racking Systems is the combination of fast order-picking and the best possible use of space. This compact construction is used in a wide variety of industries where warehousing space is limited. The variable height and depth of the shelving and height-adjustable supporting beams ensure maximum flexibility and the space-saving aisles can be worked either with man-down high-lift stackers or man-up order-picking stackers – for convenient pallet storage and retrieval or for fast order-picking straight from the pallet.
Specially designed Narrow Aisle trucks or cranes are required, to allow manoeuvring in the narrow aisles between racks. Handling equipment is often highly automated, and guided by wire or rail.
BENEFITS
- 100% accessibility to individual pallets
- Best configuration for maximum storage, density and efficiency
- Better utilisation of space
- Additional cost of specialist forklift truck offset by the added value of improved space utilisation
- Lower occupancy rates per pallet stored
TYPICAL APPLICATIONS
- Fast Order Picking
- Space Saving Solution
- Automated Handling
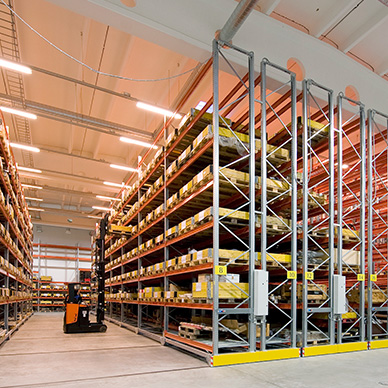
Mobile Pallet Racking
Mobile Pallet Racking Systems are the optimal solution for storage, providing dense pallet storage and helping to reduce costs for a new building or the possibility to better utilise existing warehouse storage space more efficiently.
The electronically controlled heavy duty mobile pallet racking system runs on embedded rails and can carry bay loads of up to 24 tons at racking heights of up to 12 metres, with runs up to 90m possible.
When individual aisles open, state-of-the-art sensor technology and variable control options ensure ease of operation and absolutely safety.
Thanks to a wide variety of accessories, Mobile Pallet Racking is suitable for any kind of warehoused goods and with a guaranteed operational safety at temperatures as low as -30° C it makes it ideal for use in cold storage rooms.
BENEFITS
- Maximum use of floor space – only one operating aisle
- Save up to 40% of the space required by conventional pallet racking
- Alternatively increase your storage capacity by up to 80%
- Good occupancy rates helping to reduce energy bills in cold stores
- 100% individual pallet access
- Modular design adapts to any requirement
- Safety according the European Directive 2006/42/EG and DIN EN 15095
TYPICAL APPLICATIONS
- Space Saving Solution
- Cold Storage
Carton Flow Rack Solutions
Carton flow is a vital part in the supply chain for components at assembly lines and conveyer belt lines. A picking station is constructed from a rack supplied with leaning roller tracks used to transport components to the assembly station. Wheeled tracks can also be used in warehouses as a part of the overall logistic process. Loading on one side and unloading on the opposite according the FIFO principles (First in first out).
Carton flow systems are built either as stationary units or supplied with lockable wheels allowing for fast and simple changes in warehouse layout. Loading and unloading are separated into different aisles and picking can be conducted without interruptions.
The racks are adjustable and designed from an ergonomic point of view in order to obtain efficient handling for the workers.
Storing in Carton Flow Rack systems has large economic advantages due to the fact that cartons are stored with a high packing density, releasing floor space compared with traditional storage methods, while also reducing travel distances and times between stock shelves and picking face.
TYPICAL APPLICATIONS
- Assembly Lines
- Efficiency Improvements
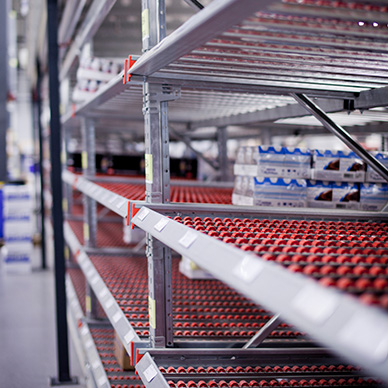
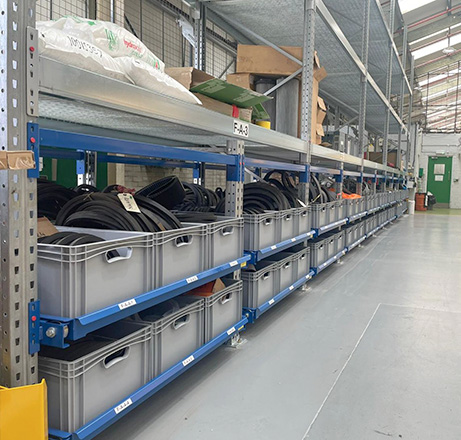
Pull Out Racking Units
The pallet racking pull-out units make it possible to move pallets backwards and forwards, similar to drawers, even with a heavy duty full load up to 1000kg.
In the extended position, a person can more easily access the entire pallet. The pull out unit therefore frees up the excessive clearance distance needed above pallets making your storage more efficient.
BENEFITS
- Increase storage capacity
- Create space
- Easy access
- Increased picking rates
- Good working environment
TYPICAL APPLICATIONS
- Storage Optimisation
- Increasing Picking Rates
Pull-Out units will save you both space and time, all while ensuring a good working environment with ergonomic picking.
Pallet Shuttle System
The Pallet Shuttle System is a semi-automated storage solution for the handling of goods inside channels similar to a Drive-In setup. The Pallet Shuttle System removes the need for forklift trucks to enter the aisles and hence offers a cost effective and time saving storage solution.
BENEFITS
- Efficient system of compact storage for warehouses with low levels of SKU
- Optimisation of storage, loading and unloading stages
- Low level of risks or stress to the warehouse operating staff
- Low level of risks or damage to the equipment -loading machinery and racks, thanks to the movement front warehouse
- Removes the need for specialist forklift trucks
All handling of the goods within the channels is carried out using the Pallet Shuttle which is remotely controlled by the user. Handling of the pallets outside of the rack is conducted using standard forklift trucks. This therefore removes the need for a forklift truck to access the storage channel.
The pallets are placed on an Pallet Shuttle (a battery powered pallet cart) which carries the pallets into the rack.
The Pallet Shuttle System can work either as FIFO or as LIFO, so it is a highly efficient alternative to Live storage and Drive-In Racking in such situations.
TYPICAL APPLICATIONS
- Cold Storage
- Food Production
- Meat Processing
- Beverage Production and Distribution
- All Drive-In / Drive-Through Racking users
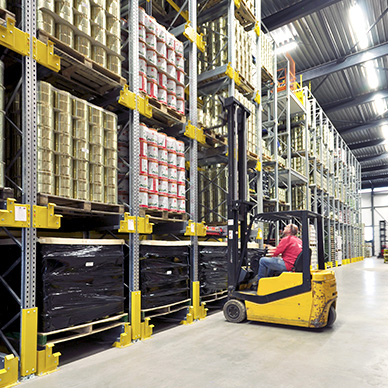
Push Back Pallet Racking Systems
Push-Back racking provides high-density live storage where quick and easy access to loads is required within your warehouse. Pallets are loaded into the racking system on telescopic trolleys (carts), each trolley being pushed back into the rack by the incoming pallet.
Pallets can be stored two, three or even four deep. Pallets are loaded and unloaded from the same aisle face, which reduces truck travel distances, and cuts cycle times.
Loaded trolleys return to the face of the rack when the previous pallet is unloaded, The unique design of Speedlock push back trolleys allows mixed product and pallet types, including poor-quality pallets, to be stored in the same rack, even in the same lane. A range of trolley sizes is available to suit all types and sizes of pallets. Colour coding of trolleys aids stock identification, and a unique multi-wheel design ensures trolleys run smoothly and reliably, even in the demanding environment of a cold store.
Push-back racking can also be used to provide additional storage space in otherwise unusable areas such as above cross-aisles or around dock levellers. When fully utilised, very high occupancy rates can be achieved, compared to Drive-In racking or Block stacking.
BENEFITS
- Quick easy access to all storage lanes
- Maximum use of floor space
- Suitable for bulk storage/cold store
- Pallets are automatically presented at the rack pick face
- Accessible by (FILO) First-In, Last-Out principle
TYPICAL APPLICATIONS
- Long & Oversize
- Storage Optimisation
- Bulk Storage
- Cold Storage
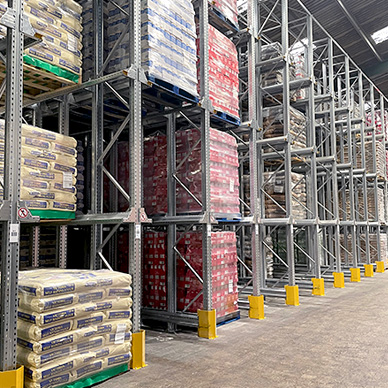
Drive-In Pallet Racking
Drive-In Racking is ideal for storing large quantities of the same type of goods: your existing space can be used up to 90% more effectively with Drive-In racking compared to standard, conventional pallet storage systems.
Drive-In Racking is suitable for goods that can be stored on pallets behind or on top of each other, but ideal when greater access is required compared to block stacking. Pallets are stacked by the first-in, last-out (FILO) principle on supports mounted on both sides of the Drive-In channels. This means that individual pallets cannot be accessed directly, but one by one from the front of the rack.
As a form of block stacking, Drive-In Racking systems significantly increase the storage density in a warehouse. Consequently, the existing space can be used up to 90% more effectively than with conventional pallet storage systems.
Drive-In Racking eliminates the need for loading and picking aisles. The lift truck positions pallets on front-to-back rails, allowing rows to be stacked next to each other. Drive-In racking provides a safe and efficient equivalent of block stacking for loads which are too fragile or unstable to be stacked on top of each other.
BENEFITS
- High density storage – maximising cubic space
- More pallets stored per cubic metre than any other storage system
- Limited stock rotation – particularly suitable for seasonal goods
- Ideal for cold and chill storage applications
- Accessible by the First-In, Last-Out principle
- Used for bulk goods of the same type
TYPICAL APPLICATIONS
- Storage Optimisation
- Bulk Storage
- Cold Storage
Efficiency & Safety
When designing and implementing a pallet racking, safety and simple access both for products and your team are paramount to it’s successful integration.
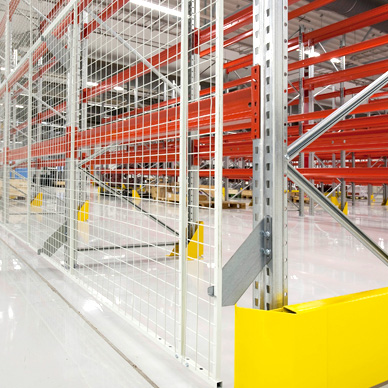
Anti Collapse Mesh
A mesh safety screen which helps prevent accidents whilst handling and storing goods.
This screen as a general rule is used at the rear of pallet racking where goods may potentially fall onto personnel, but can be used for other applications.
Panels are available in 3 sizes, with a choice of 100 x 50mm, 50 x 50mm or 25 x 25mm mesh. Various sizes of stand-off brackets are available.
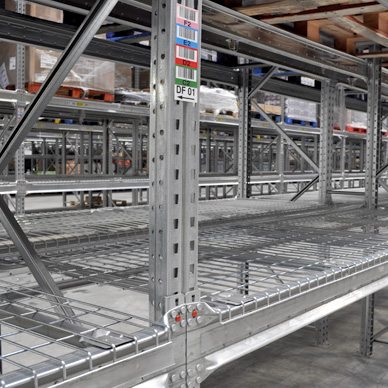
Mesh Decking
Sitting on the pallet racking beams mesh decking acts as a shelf offering an alternative to timber decking and solid steel panel solutions.
- Small Carton Picking
- Non Standard Pallets
- Protection under Tunnel Bays
- Even Air Distribution in Chilled Storage
- Improved Light & Sprinkler Penetration
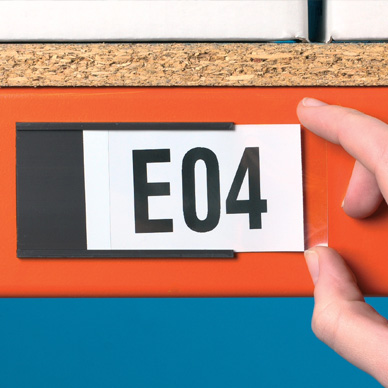
Labelling
Clarity of purpose and safety are important in any warehouse. We provide complete sign and marking solutions for your racking and warehouse.
- Emergency, Health & Safety Signs
- Beam & Shelf Location code labelling
- Aisle & Bay Markers
- Weight Load Notices
- Floor Markers
Design & Installation
After an initial consultation and site visit our advisers will recommend and submit a design for a racking system that will meet your needs and enhance your productivity. Our specification team includes SEMA approved, SARI certified rack inspectors to ensure compliance and the safety of your workforce.
Whether you’re looking to replace existing an industrial racking system or need a complete new turnkey warehouse solution we have the experience and expertise to design, install and maintain. In short we offer a guaranteed peace of mind racking solution for your business.
To complement our partitioning offering we also provide space planning and design services, providing full fit out and refurbishment of office, shelving and other work space requirements.
Installation of your racking is arranged as quickly as possible or to your own rollout schedule to suit your requirements minimising disruption to your business operation.
Pallet Racking Projects

Very Narrow Aisle (VNA) Racking Optimisation
FOOD & DRINK
An international ingredients supplier maximises pallet storage and protection in a complete turnkey solution.
RACKING
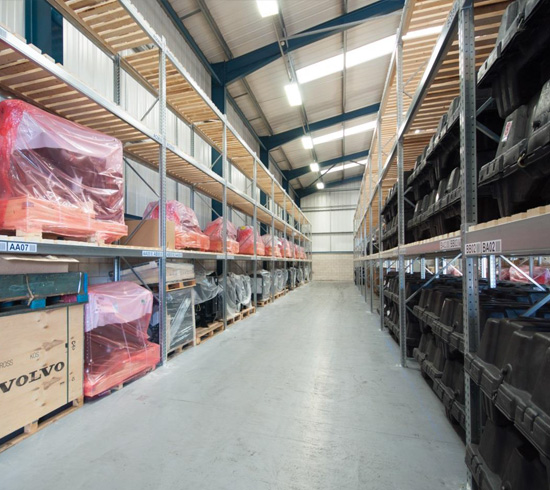
Vertical Storage Creates Nationwide Inventory
AUTOMOTIVE
An engine transmission manufacturer maximises floor space and consolidates small parts from around the country.
RACKING
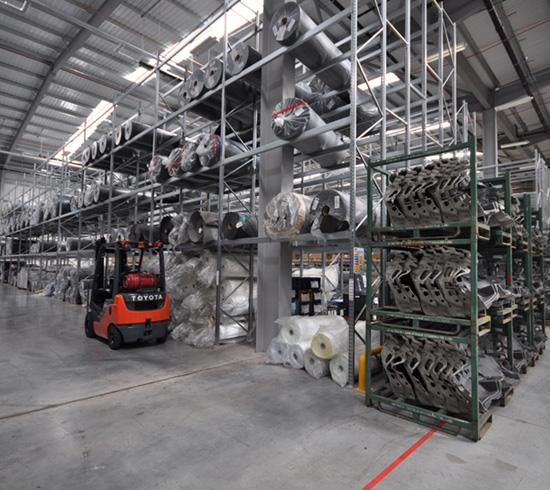
Automotive Interior Storage
AUTOMOTIVE
An engine transmission manufacturer maximises floor space and consolidates small parts from around the country.
RACKING
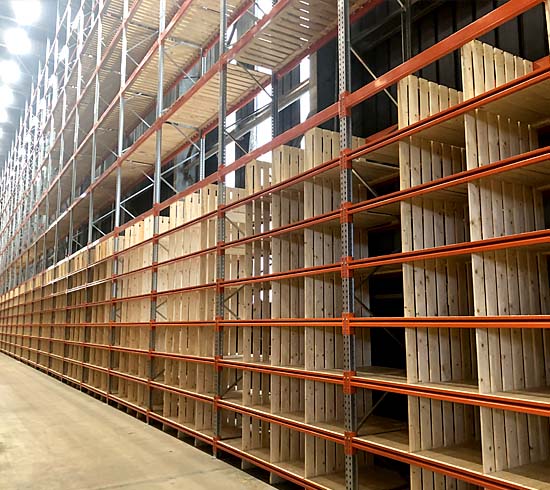
Racking Partitioning for Split Case Picking
HYGIENE
Wide aisle racking with timber decking improves e-commerce picking rate for bathroom & sanitary ware company.
RACKING
Are your warehouses being used as effectively as possible?
The answer is probably no…
Most organisations can improve the efficiency of their facilities, whether as part of a periodical usage audit or a strategy for expansion and service improvement. Storage space utilisation, products accessibility, as well as the movement of people and stock throughout the whole site.